Success Story
AAK
Cutting energy and water consumption by 10%, saving approximately 10 million kWh per year.
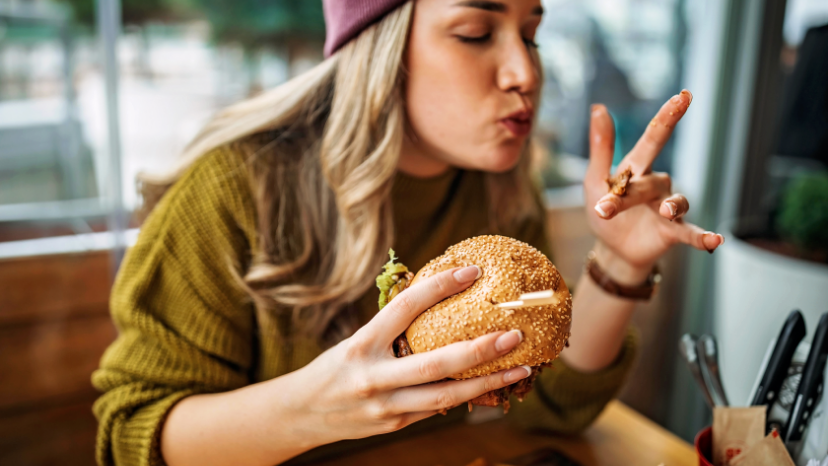
The Challenge
AAK is the world’s leading producer of refined vegetable fats. Its 60,000m² production facility in Hull runs 24/7. Equipment is powered by compressed air, steam and motors that consume vast amounts of energy — so saving energy can have a huge impact on overheads and the environment.
AAK commissioned us to review its energy consumption and spend. The results revealed the potential for wide-ranging savings in terms of:
- Increased energy efficiency.
- Reduced overheads.
AAK challenged us to deliver.
The Solution
AAK has miles of pipes distributing compressed air across the site. When compressed air systems spring a leak they have to work harder to compensate, and the effect on your energy bills can be profound.
We inspected the system, identifying several leaks. Fixing these and reducing the air intake temperature to the compressors has saved a million kWh a year across this system alone.
Steam generation is also an essential part of AAK’s production, and a prime contributor to the organisation’s energy costs. Our audit identified that leaks and missing or damaged insulation was reducing efficiency and costing AAK almost seven million kWh every year. Improvements to this system paid for themselves in just eight and a half months.
Realising the full potential of energy-saving opportunities involves more than just mechanics. It’s about making energy matter to your organisation, so that everyone shares a vested interest in spotting and fixing leaks or suggesting the next efficiency saving. We’ve helped AAK devise and implement a comprehensive energy management policy, which included the establishment of an energy committee to raise energy awareness and make it a core component of day-to-day operations.
We delivered a training programme to help staff understand the difference they can make in their daily work. And sub-metering data is measuring the effectiveness of the policy across the manufacturing process.
The Benefits
In establishing a measure of consumption against production, we’ve helped AAK understand and control its baseload demands and enhance its efforts to meet climate change commitments.
As well as optimising efficiency in its compressed air and steam generation systems, we looked at its electrical motors too — how often are yours needlessly running at full power? Replacing control and throttling valve systems, and controlling motor speeds with variable speed drives has saved AAK almost a further million kWhs a year, and these changes have paid for themselves in less than three years.
In total, the improvements and changes implemented are now saving AAK approximately 10 million kWh per year.
Trident has identified savings approaching 10% of our energy and water costs.”
John Officer - Director of Operations, AAK
Trident has identified savings.”
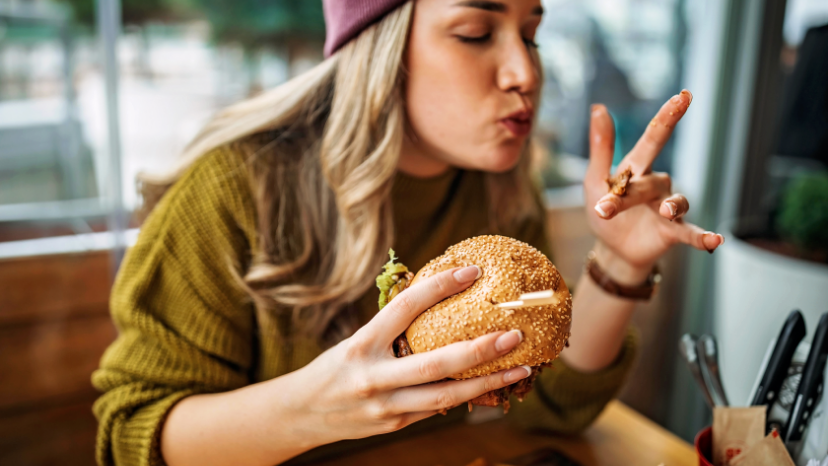